It may have been the Fourth of July, but it was a Japanese titan of the car that set off the fireworks a few weeks ago in the auto industry.
The company—and its new CEO, Koji Sato—unveiled ambitions to halve the size, cost, and weight of batteries for its electric vehicles (EVs) following a breakthrough in its solid-state battery technology.
This is going to be huge…
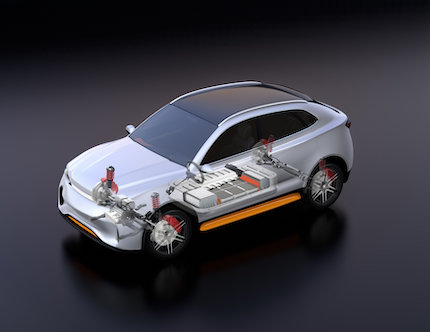
Toyota’s Battery Breakthrough
I’m talking about none other than Toyota Motor Corp. (TM), of course. The company’s ambitions came into focus after the world’s largest automaker by sales surprised investors in June with plans to commercialize its solid-state battery technology in an electric vehicle later this decade. Toyota is working on the technology with Panasonic through their joint battery venture.
Solid-state batteries have long been hailed by industry experts as the most promising technology to solve EV battery problems such as charging time, capacity, and the risk of catching fire. These batteries replace a liquid electrolyte with a solid one and use lithium metal at the anode instead of graphite, the current standard in lithium-ion batteries.
Toyota’s breakthrough would allow an EV powered by a solid-state battery to have a range of 1,200 kilometers (745 miles) and charging time of 10 minutes or less. That is 2.4 times the range of conventional liquid electrolyte batteries. And the Tesla Inc. (TSLA) Supercharger network—the largest of its kind—offers the equivalent of 200 miles, from a 15-minute charge.
Toyota said it should be able to mass produce, commercialize, and mount solid-state batteries in vehicles as early as 2027.
And there were more revelations from Toyota, which is finally serious about meeting the challenge from Tesla.
“Gigacasting”
As Toyota turns its attention to EVs, it plans changes to save time and money. These changes depart radically from the assembly line-driven process that has dominated the automotive industry since Henry Ford and Ford Motor introduced the first one in 1913.
Toyota aims to use its new “gigacasting” production method to build a new electric vehicle model due out in 2026. Gigacasting combines many of the small components that make up a vehicle’s frame into a single piece of molded aluminum, drastically streamlining the manufacturing process.
The company envisions its EV bodies to made up of just three sections: front, middle, and rear. Gigacasts will be used for the front and rear sections. A prototype of the rear section combined 86 individual sheet metal parts that normally would be assembled across 33 steps into a single large structure, and the automaker expects to do the same for the 91 components in the front end.
Toyota understands that the high cost of batteries makes it tougher to turn a profit from EVs than their gasoline-fueled counterparts, so cost-cutting in other parts of the manufacturing process is crucial if it’s going to compete. Toyota says it aims eventually to halve the number of steps in the production process as well as spending on manufacturing equipment.
Gigacasting is the very centerpiece of this plan. Along with a self-propelled production line, it will do away with assembly line conveyor belts entirely.
With the self-propelled production line, the chassis is assembled up to the point where the motor and battery can be installed, after which the partly finished car can drive itself through the rest of the production process.
If gigacasting sounds familiar, it should. It is Toyota’s answer to the megacasting technology that Tesla began using for its Model Y in 2020. Tesla cut the production cost of its EVs by half between 2017 and 2021, according to Goldman Sachs, and now earns nearly five times as much net profit per electric vehicle as Toyota.
More benefits of megacasting may be coming too. The cost of an EV frame can drop much more if the lower and upper halves of the body are each cast as a single part, for example.
Toyota’s Three-Step Plan
Toyota is currently in stage one of its new plan as announced by Sato. The second part of the plan will come around 2026, and the final efforts will be in place by 2030. Toyota aims to produce some 1.5 million EVs globally by 2025 and 3.5 million by 2030. If all goes well with its plan, improved productivity and economies of scale will mean lower prices, which should work to drive EV sales volume for Toyota.
In its second step, Toyota will integrate the Arene automotive operating system, which is currently being developed by its software arm, Woven. Keep in mind that today’s successful EV makers, like Tesla, are just as much software companies as they are automakers.
Finally, the third step will be the culmination of the automaker’s combined plans and efforts. Sato says Toyota will transition to a new structural body and layer the Arene operating system with updated software services. With the new body will also come a re-engineered purpose-built EV platform that maximizes space, performance, and efficiency.
Will this three-step plan allow Toyota to beat Tesla in the EV race? It’s unlikely, but possible.
However, if Toyota does indeed have a breakthrough regarding solid-state batteries, it could be a game changer for the entire auto industry. Even if it doesn’t beat out the competition, its shareholders will benefit from its long-delayed and serious entry into the EV market, thanks to the strategy shift being implemented by the new CEO.
Toyota’s stock is up 18% year-to-date, with all of that gain coming in the past few months after its EV plans were revealed. I believe the stock is a good buy anywhere in the 155 to 170 range. And you collect a 2.6% dividend yield, too.